
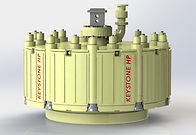

INNOVATION
Introducing the 2nd Generation of Keystone HP Cluster Drills. Designed specifically for low-headroom, large diameter (24” to 144”) rock drilling applications for the Construction and Foundation Industries. Many drilling contractors utilize drill rigs with limited height clearance such as fixed height rotaries, telescoping Kelly Bars, or require shorter drills to clear protruding casing. Implementing a Cluster Drill was physically impossible in these applications. The 2nd Gen HP Cluster Drill offers a solution that creates many opportunities for hammer drilling with low clearance rigs/applications. The 2nd Gen HP stands just 58” tall, making it the shortest Cluster Drill in its class. Rigs with an Air Kelly only require 5’ of clearance, Kelly to ground, with the 2nd Gen HP. Also, with the HP’s integrated “Ratchet” air inlet, we eliminate the need to add an extra height adding “Ratchet” sub. Rigs not setup for air can operate with as low as 6’ of clearance, Kelly to ground, in “Ratchet” drilling applications.
​
Despite our reduction in height, we did not reduce the industry leading performance and productivity of the HP Cluster Drill. We continue to utilize the CS8 Hammer and 10” patented quick change bits. We also optimized our bit layout leading to greater penetration rate and extended tooling life. Also, we added internal structural reinforcement to match the torque output of the larger, more powerful rigs. With the creation of the 2nd Gen HP we hope to open many previously unattainable opportunities for our large diameter rock drilling customers.
​
In addition to height restrictions, another difficulty facing many of our customers is space needed for multiple air compressors on a drill site as well as mobilizing multiple compressors from hole to hole. In response to this issue, Keystone has developed the Cluster Core Barrel which only places hammers on the gauge row with a hollow center. The drill excavates a 10” kerf approximately 4 feet in depth and leaves a rock core much like a traditional core barrel. Once to depth, the rock core must be broken and removed with traditional drilling tools before the Cluster Core Barrel can advance. A 48” diameter hole can be drilled with as little as one 1600 SCFM compressor using only 3 bits and hammers. Typically, a 48” full face Cluster Drill requires (3) 1600 SCFM compressors with 7 bits and hammers so there is great potential for saving in fuel, compressor rental costs, mobilization time, bits, hammers, spare parts, etc.
​
The Cluster Core Barrel is also designed for low headroom applications with as little as 6’ of clearance required for “Ratchet” drilling which includes the Kelly box. Also, there is no need to perform a full rotation in “Ratchet” drilling. A 3 hammer Cluster Core Barrel only needs to oscillate back and forth a third of a rotation to achieve full hammer coverage of the kerf bottom.
​
All air drillers know the challenges in fitting compressors on drill sites as well as the time- consuming mobilization from hole to hole often across rugged terrain. Since the Cluster Core Barrel only implements hammers on the gauge row, the overall number of hammers is reduced drastically. Fewer hammers means less compressors and less hassle and expense.
​
Cluster Drills are often overlooked in the larger hole diameter applications due to the rising number of hammers, bits, and compressors needed to complete the job. Keystone’s solution is to divide the job into 2 or even 3 steps by implementing Hole Openers. By drilling a smaller pilot hole and then stepping up to a larger Hole-Opener to complete the full diameter, a driller can divide the number of hammers, bits, and compressors in half of what it would require for a full-face drill. We always recommend separating the drilling area in equal steps, so the same number of hammers and air compressors are used for each stage. The Hole-Opener consists of bits and hammers on the outer diameter and a pilot ring on the inner diameter to guide the hole opener along the original pilot hole. Often, customers will already own a full-face Cluster Drill that they would like to use for the pilot hole. This is no problem as we will custom design Hole-Openers up to 144” in diameter to meet your specifications.
SUPPORT MODULE

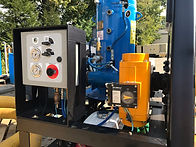

Safety and efficiency. Two very important factors the modified Support Module were designed to achieve. This safer and more efficient design places the controls in the hands of the rig operator, creating distance between personnel and multiple hose connections. By utilizing Bluetooth technology, the Support Module outlet air is controlled via a smart device, at a distance of over 150 feet. Despite the addition of the remote capability, the Support Module maintains the ability to be controlled manually
at the panel.
​
The Keystone Support Module combines an air manifold, lubricator and water injection all on a single platform. The air manifold offers five, 3” compressor connections that are designed to optimize air flow through the ASME Certified Pressure Vessel. The Support Module incorporates a lubricator and water injection system, both with fully adjustable flow control to meet the application’s needs.
​
Safety is a priority to Keystone, however, risk will always accompany high-pressure hose connections. Since the connection is necessary, we created distance between the operator and reduced the potential risk by incorporating remote control of the outlet valve. Utilizing an App developed by Keystone, the operator can use their personal Android device, or a supplied tablet to control the Support Module. The operation includes opening, closing and emergency-close function. The remote emergency-close feature closes the outlet valve within 5 seconds. This feature allows the operator to eliminate air flow in the event of an emergency, from a distance of over 150 feet from the Support Module. Upgrades to the injection systems include pilot controlled valves that open when the system is pressurized, and close when outlet valve is closed. With this added feature, a bypass valve is added to the water injection system to redirect the water when the pilot valve is closed. This provides automated lubrication and water flow without the attention of an operator.
​
Keystone strives to continually improve our products and create a safer environment for our customers. The Support Module can also be configured to meet your needs. Various connection sizes may be used at the air manifold, larger outlet orifice at the discharge pipe, and any additional monitoring devices can be tailored to fit.
If you'd like to discuss the capability of providing a safer and more efficient site with our Remote Controlled Support Module contact Keystone Drill Services today.